Ślad węglowy materiałów budowlanych i jego wpływ na emisyjność budynków oraz budowli
Do produkcji materiałów budowlanych zużywamy zasoby naturalne naszej planety i wykorzystujemy energię. Zagrożenie przeludnieniem oraz efekt globalizacji stają się wyzwaniem dla nas wszystkich. Nigdy w historii Ziemi nie mieszkało na niej tylu ludzi potrzebujących dla siebie „dachu nad głową”. Zapotrzebowanie na materiały budowlane stale rośnie, co nie jest bez znaczenia dla całego ekosystemu. W wyniku emisji gazów cieplarnianych przez różne gałęzie przemysłu temperatura na naszej planecie wzrasta, co pociąga za sobą olbrzymie zmiany w naszym otoczeniu. Zmienia się drastycznie klimat, tereny zielone ulegają stepizacji – wszystko to ma wpływ na inne zjawiska pogodowe, takie jak ulewne deszcze, powodujące podtopienia, czy trąby powietrzne, które do niedawna w naszym kraju nie występowały. Przykładem może być, chociażby nawałnica, która przeszła przez Pomorze w sierpniu 2017 r., powodując liczne zniszczenia. Wiatr podczas niej wiał z prędkością 120 km/h.
Sektor przemysłu produkujący materiały budowlane ma niezaprzeczalnie swój udział w tym procesie, jednak emitentów CO2 jest zdecydowanie więcej.
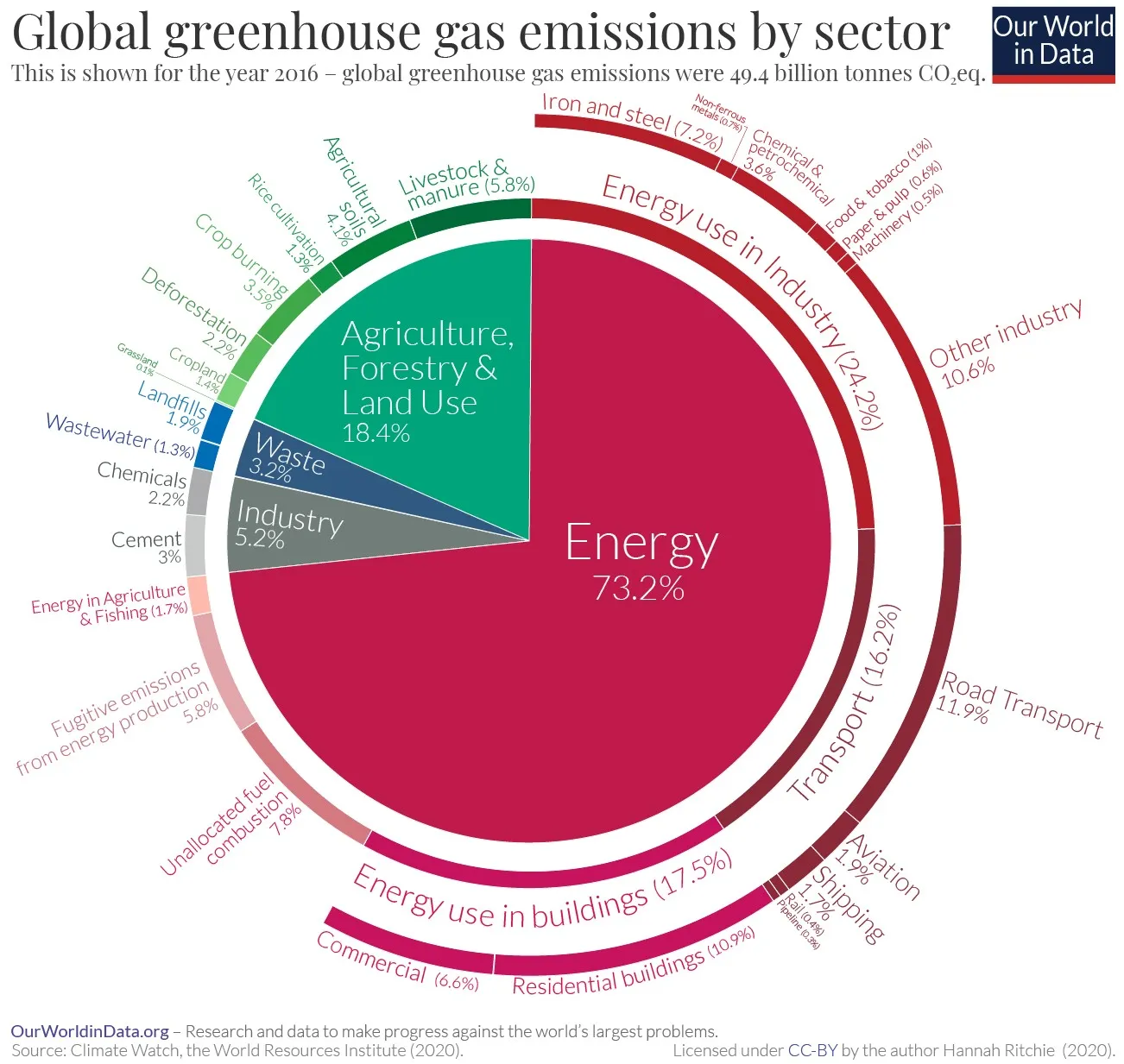
Rys. 1. Globalna emisja gazów cieplarnianych dla poszczególnych sektorów gospodarki
Źródło:https://ourworldindata.org/emissions-by-sector
Rysunek 1 pokazuje, że w tej nadmiernej eksploatacji Ziemi udział biorą wszystkie branże, bez wyjątku. Emisje pochodzące z energii w 2016 r. stanowiły 3⁄4 całej puli. Dzisiaj i w przyszłości wartość śladu węglowego materiałów budowlanych zależy i zależeć będzie głównie od tego, w jaki sposób będziemy produkowali energię elektryczną, konsumowaną zarówno w procesach produkcyjnych materiałów budowlanych, innych procesach, jak i w transporcie, czy też energię zużywaną przez budynki do tego, aby zasilać wszelkie systemy i instalacje, w które zostały one wyposażone.
Emisje procesowe w przemyśle cementowym i chemicznym stanowią zaledwie 5,2% całości globalnej emisji GHG (rys. 1). Dla cementu wartość ta wynosi 3% i jest to emisja procesowa wynikająca z rozkładu węglanu wapnia na tlenek wapnia – w tym procesie efektem ubocznym jest powstawanie CO2 (CaCO3 CaO + CO2). W samym procesie produkcji klinkieru używanego do wytwarzania cementu emisja procesowa stanowi ok. 63% śladu węglowego.
Ślad węglowy materiałów budowlanych zależy w dużej mierze od źródła energii elektrycznej i cieplnej użytej w procesie produkcji, a co za tym idzie – od struktury paliw stosowanych przy wytwarzaniu energii elektrycznej. Zależność ta wprost wpływa na emisyjność materiałów budowlanych.
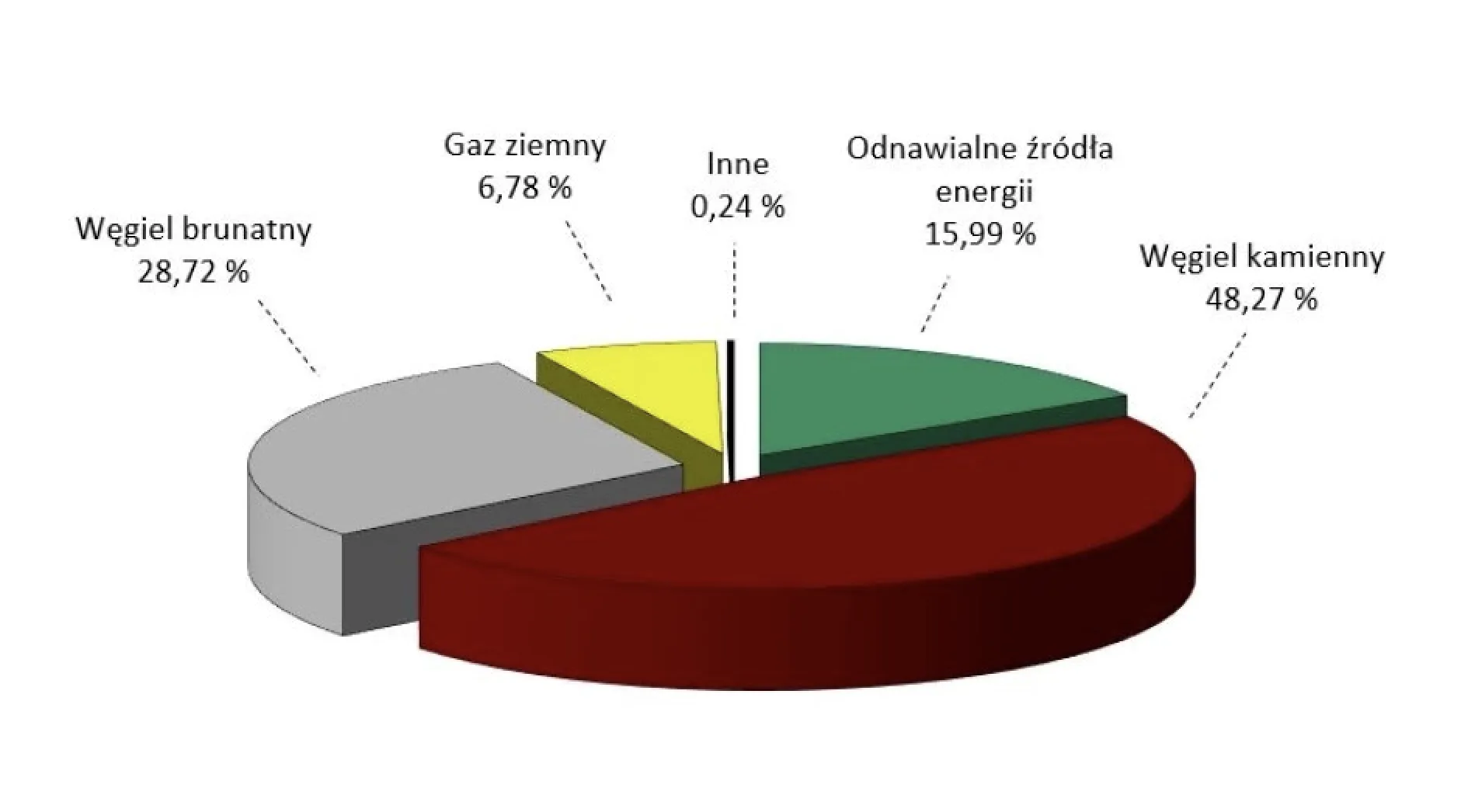
Rys. 2. Struktura paliw i innych nośników energii pierwotnej zużytych do wytworzenia energii elektrycznej sprzedanej przez PGE Obrót SA w 2022 r.
Według oficjalnych danych PGE Obrót SA z 2022 r. do energii produkowanej w Polsce w 76,99% używany jest węgiel. Odnawialne źródła stanowią w tej strukturze zaledwie 15,99%. (rys. 2). Od tego wszystko się zaczyna, ponieważ każdy producent materiałów budowlanych (nie dotyczy to firm produkujących lub pozyskujących energię z OZE) do obliczeń śladu węglowego dla swoich produktów przyjmuje właśnie taką strukturę paliw.
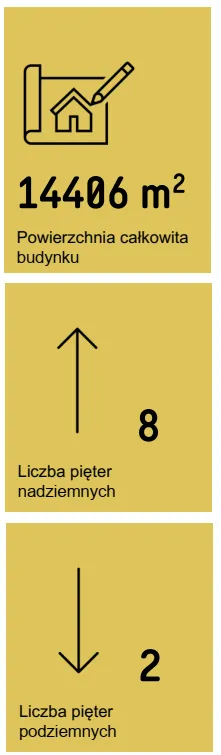
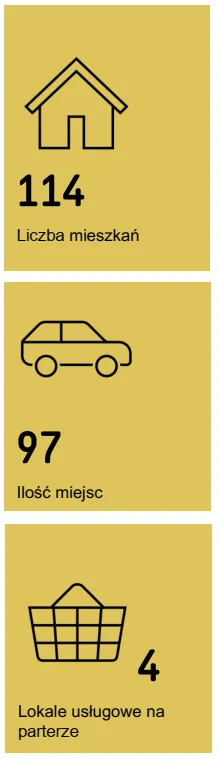
Rys. 3. Schemat oraz parametry rozpatrywanego budynku poddanego analizie LCA (life cycle assessmnt)
Źródło: Analiza własna. Raport LCA: Budynek mieszkalny wielorodzinny w Krakowie
Na rysunku 3 znajduje się charakterystyka rozpatrywanego budynku. Rozpatrując ślad węglowy materiałów budowlanych, musimy spojrzeć na problem szerzej i uwzględnić tę jego część, którą generują powstające obecnie budynki. Z analizy struktury energii elektrycznej wynika, że ślad węglowy wszystkich materiałów budowlanych wykorzystanych do wznoszenia budynków to zaledwie 20-30% całej emisji, jaką generują budynki we wszystkich fazach ich powstawania w zaplanowanym 50-letnim cyklu życia. 70-80% emisji to ślad węglowy wynikający z użytkowania budynku oraz jego napraw. Oznacza to, że materiały budowlane odpowiadają tylko za 1/3 śladu węglowego (wbudowany ślad węglowy) powstającego w fazie wznoszenia i użytkowania budynków. Aby lepiej zrozumieć zagadnienie i zobrazować sobie alokację śladu węglowego w procesie budowy, użytkowania i utrzymania budynku, posłużmy się przykładem konkretnego budynku mieszkalnego wielorodzinnego w Krakowie, na bazie którego przygotowaliśmy analizę LCA (life cycle assessment).
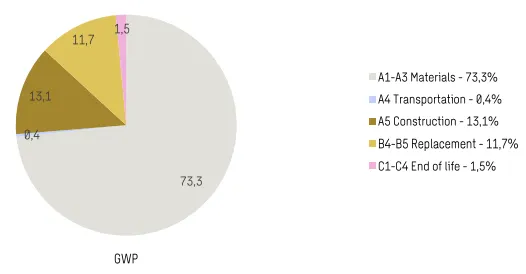
Rys. 4. Ślad węglowy materiałów budowlanych oraz poszczególnych faz budowy z wyłączeniem fazy eksploatacji (B1–B3)
Źródło: Analiza własna. Raport LCA: Budynek mieszkalny wielorodzinny w Krakowie.
Z analizy rozpatrywanego przypadku (rys. 4) wynika, że po wyłączeniu faz życia budynku związanych z użytkowaniem, utrzymaniem oraz naprawami (fazy B1–B3) 73% śladu węglowego pochodzi z materiałów budowlanych. To bardzo duża część, niemniej trzeba pamiętać, że odnosi się ona wyłącznie do fazy budowy i zakończenia cyklu życia budynku (A1–A5; B4–B5; C1–C4). Pozostała część dotyczy m.in. transportu, procesu budowy oraz utrzymania placu budowy i rozbiórki.
Kiedy spojrzymy na problem z innej perspektywy, tzn. weźmiemy pod uwagę sumę elementów w całym cyklu – od wzniesienia aż do zakończenia życia budynku – to widzimy, że materiały użyte do jego budowy stanowią zaledwie 21,3%, a użytkowanie, utrzymanie i naprawy to 70% śladu węglowego. Schodząc jeszcze niżej, możemy zauważyć, że lwią jego część generują dwa materiały: beton (10%) i stal (6%). Informacje te wskazują nam obszar, w którym powinniśmy szukać potencjalnej redukcji wbudowanego śladu węglowego. Pogłębiając analizę, zadaliśmy sobie pytanie, który z elementów konstrukcyjnych odpowiada za największy ślad węglowy. Odpowiedź brzmi (i nie jest to żadne odkrycie): ten, który zawiera najwięcej betonu i stali, czyli płyta fundamentowa. W omawianym przypadku płyta fundamentowa (przywołanego w tej części artykułu budynku wielorodzinnego w Krakowie) odpowiada za 755 446 kg e CO2 – 19,9% śladu wszystkich materiałów budowlanych i 5,5% w całym cyklu życia budynku. To kolejna sugestia, gdzie należy szukać optymalizacji emisji CO2. Zastosowanie betonu niskoemisyjnego oraz wymiana części zbrojenia strukturalnego na zbrojenie rozproszone może zredukować ślad węglowy dla samej płyty fundamentowej o 42-60%. Z całą pewnością jest to kierunek, w którym powinniśmy podążać – zwracajmy uwagę na ślad węglowy wbudowanych materiałów budowlanych, a w szczególności tych o największym potencjale do optymalizacji. W naszych dalszych rozważaniach, poszukując sposobów ograniczenia emisji gazów cieplarnianych, za które odpowiadają materiały budowlane (greenhouse gas, GHG), skupiliśmy się na dwóch najbardziej powszechnych materiałach, tzn. na cemencie i betonie.
Cementy niskoklinkierowe
Emisyjność wyprodukowania tony klinkieru portlandzkiego przy obecnym miksie energetycznym to około 800 kg e CO2. Wiadomo, że emisyjność cementu jest pochodną ilości użytego do jego produkcji klinkieru. Rozwój nowoczesnych spoiw hydraulicznych zmierza w kierunku znacznej redukcji klinkieru portlandzkiego w ich składzie. Jest to spowodowane porozumieniem na poziomie Unii Europejskiej, rachunkiem ekonomicznym, ale przede wszystkim zobowiązaniami w ramach porozumienia „Fit for 55”. Porozumienie to przewiduje redukcję emisyjności GHG o 55% w stosunku do wartości z 1990 r., aby osiągnąć neutralność klimatyczną do 2050 r. Produkcja cementu bazuje na zharmonizowanej normie PN-EN 197-1: 2012, która definiuje możliwe rodzaje i odmiany cementów, jakie mogą być wprowadzone do obrotu. Daje ona duże możliwości w zakresie wytwarzania cementów niskoklinkierowych oraz doboru stosownych dodatków mineralnych do produkcji cementu. Coraz częściej w ofertach cementowni pojawiają się cementy pucolanowe CEM IV oraz cementy wieloskładnikowe CEM V, których ślad węglowy jest wyraźnie niższy od cementów portlandzkich CEM I – nawet o 40%. Cementom niskoklinkierowym przychylna jest również norma PN-EN 197-5:2021[1], która rozszerza możliwość produkcji cementu o cementy portlandzkie wieloskładnikowe CEM II/C, o zawartości klinkieru w przedziale 50–64%, oraz cementy wieloskładnikowe CEM VI, o zawartości klinkieru pomiędzy 35–49% (tab. 1).
Tabela 1. Nowe rodzaje cementów powszechnego użytku wg PN-EN 197-5:2021[1]
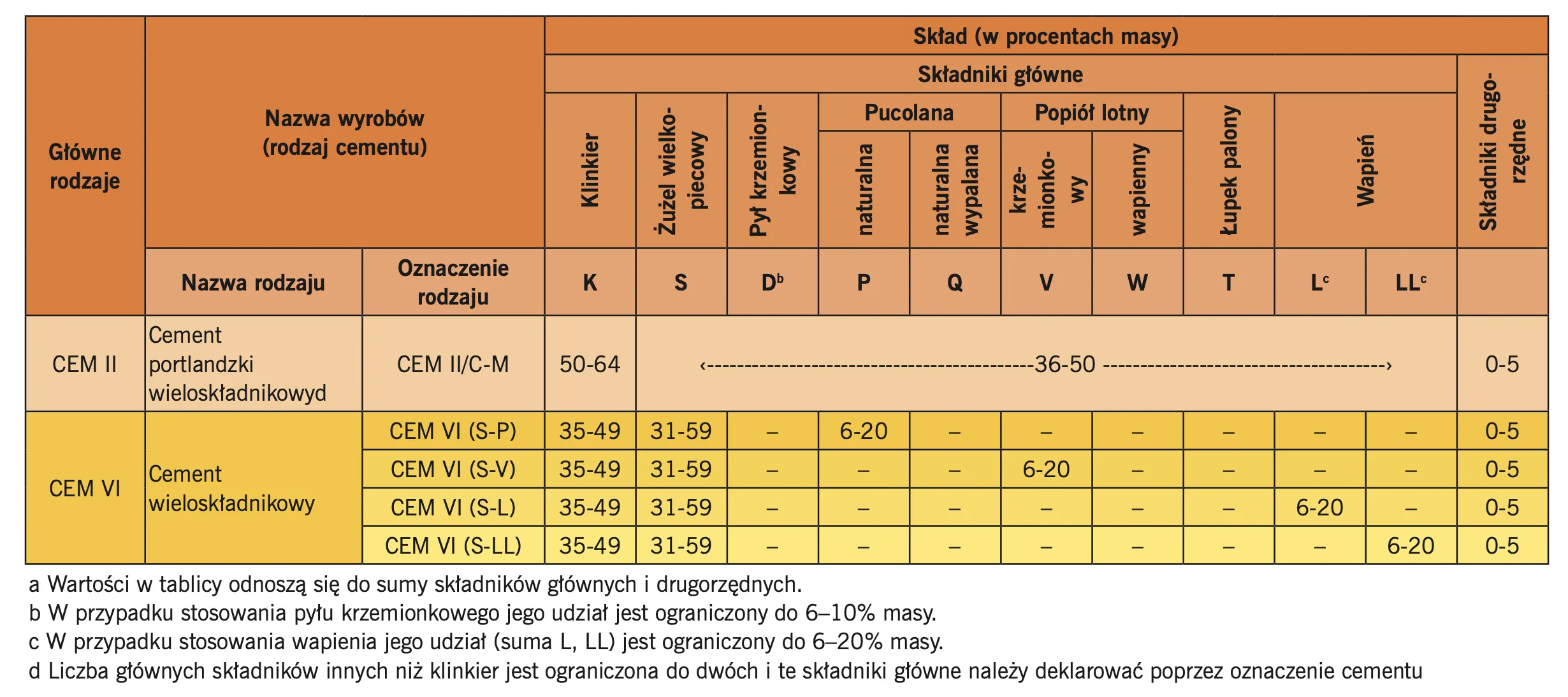
Jako uzupełnienie klinkieru w składzie cementu powszechnie stosowane są (w różnych konfiguracjach, zgodnych z wymaganiami normy) popioły lotne, żużle wielkopiecowe oraz kamień wapienny, a niebawem będzie to także gruz betonowy (symbol „F”), pochodzący z zakładów produkcji kruszyw z recyklingu. W kwietniu br. Europejski Komitet Normalizacyjny ustanowił stosowną normę EN 197-6:2023 „Cement – Part 6: Cement with recycled building materials”.
Ślad węglowy cementów można zmniejszyć, ograniczając zawartość klinkieru w ich składzie poprzez wprowadzanie do oferty cementów CEM IV, CEM V, CEM II/C oraz CEM VI. Innym kierunkiem rozwoju oferty cementowni w Polsce jest wprowadzanie cementów szybkosprawnych CEM II/A lub trójskładnikowych cementów CEM II/A-M, które zawierają mniejszą ilość klinkieru niż cementy czyste portlandzkie tej samej klasy, natomiast posiadają takie same lub lepsze parametry, takie jak wytrzymałość wczesna, a także początek oraz koniec wiązania. Cementy te dorównują powszechnie kiedyś stosowanym np. w segmencie prefabrykacji cementom CEM I 42,5 R lub CEM I 52,5 R, lub przewyższają je swoimi właściwościami. Obecnie cementownie dążą do eliminacji lub istotnego ograniczenia produkcji cementów wysokoklinkierowych. Zakładamy, że taki trend utrzyma się w przyszłości i wszyscy użytkownicy cementu zaakceptują go z korzyścią dla ochrony klimatu. Parametrem, który wskazuje ilość zużywanego klinkieru w cemencie, jest tzw. wskaźnik klinkierowy. Aby zobrazować nieuchronny kierunek zmian i ich dynamikę, na rysunku 5 przedstawiliśmy średnioroczny wskaźnik klinkierowy dla jednej z polskich cementowni. Zmiany w tym zakresie na przestrzeni 4 ostatnich lat są mocno zauważalne.
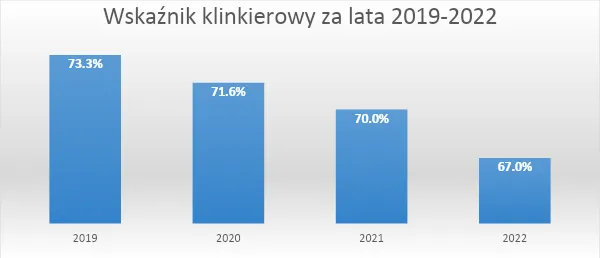
Rys. 5. Zmiana wskaźnika klinkierowego na przestrzeni lat 2019–2022
Betony niskoemisyjne
Ponieważ cement odpowiada za ponad 50% całkowitej emisji betonu, na ogół w produkcji betonów niskoemisyjnych używa się cementów niskoemisyjnych, np. CEM IV/B (V) 42,5 N-LH/NA czy CEM V/A (S-V) 42,5 N-LH/HSR/NA. Z produkcją takich betonów wiąże się (z powodu braku praktycznych doświadczeń) kwestia ich trwałości. Z pomocą przychodzą obecnie znormalizowane metody badawcze dotyczące np. badania karbonatyzacji betonu lub wyznaczania migracji jonów chlorkowych w betonie. Pomocne są również badania symulujące często spotykane warunki korozyjne betonu i stali zbrojeniowej w elementach żelbetowych. Dodatkowo norma PN-EN 206[2] definiuje koncepcję równoważnych właściwości użytkowych, którą można wykorzystać do oceny trwałości betonów niskoemisyjnych. W skrócie polega ona na udowodnieniu nie gorszej trwałości betonu testowanego w porównaniu z betonem referencyjnym wykonanym zgodnie z wymaganiami składu podanymi w tablicy F1 normy PN-B-06265:2022-08[3], przywołanymi w tabeli 2, przy czym skład betonu testowego może wykraczać poza te wymagania w zakresie rodzaju i zawartości cementu, wskaźnika w/c oraz zawartości powietrza.
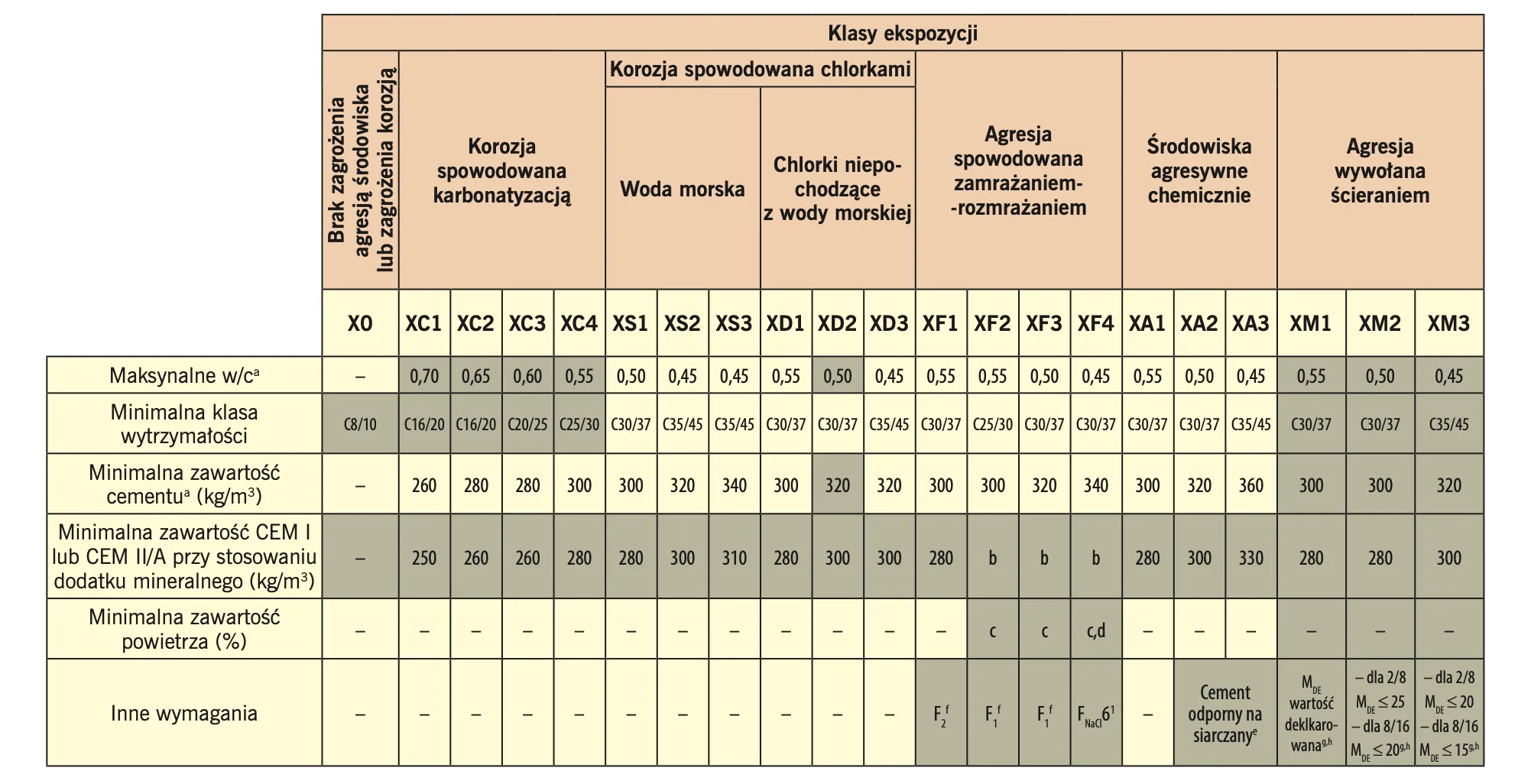
2. Tablica F1 normy PN-B-06265:2022-08
Powyższą koncepcję wykorzystano do oceny trwałości betonu wykonanego na cemencie niskoklinkierowym CEM IV/B (V) 42,5 N-LH/NA w klasie ekspozycji XC4 oraz XD1, którego przydatność zastosowania w ww. klasach ekspozycji, wg tabeli informacyjnej F2 normy PN-B-06265:2022-08[3] (której właściwy fragment przywołano w tabeli 3) należy udowodnić.
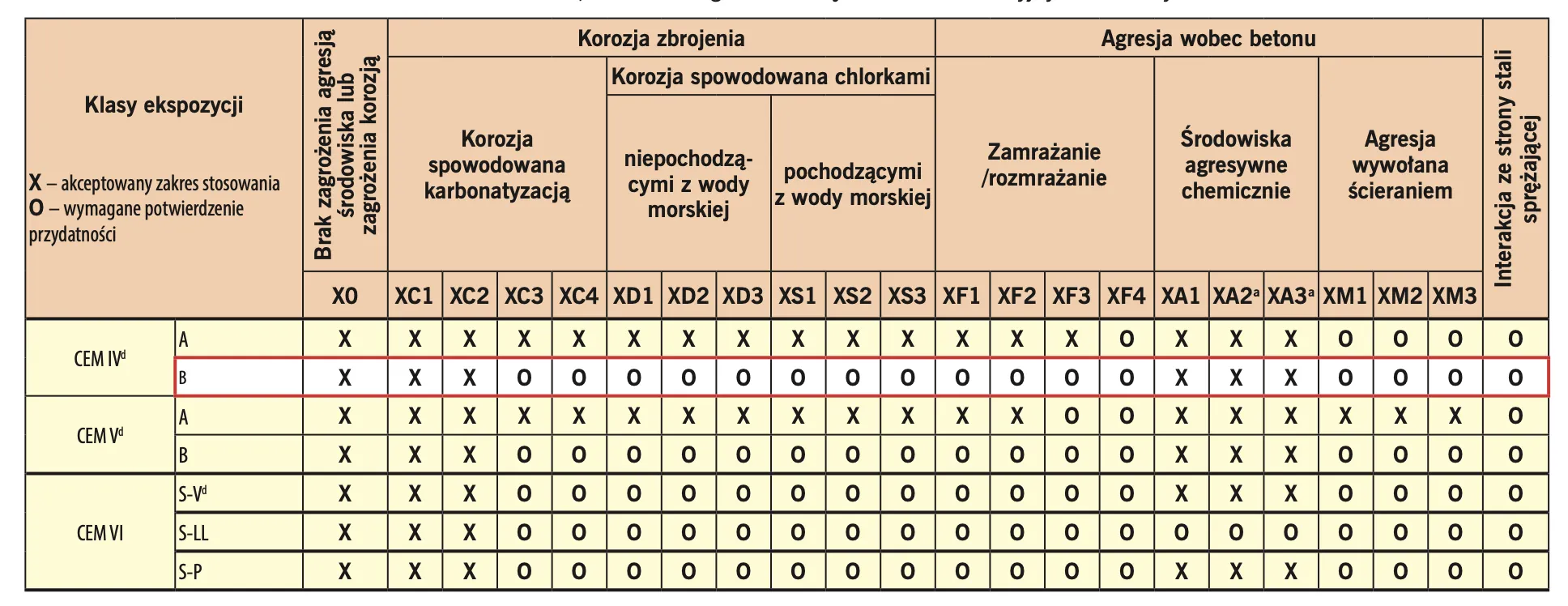
Tabela 3. Obszar zastosowania cementu CEM IV/B (V) 42,5 N-LH/NA zgodnie z załącznikiem informacyjnym F2 normy PN-B-06265:2022-08
Receptury zawierały tę samą ilość cementu, ten sam wskaźnik w/c oraz rodzaj kruszywa i jego uziarnienie.
Dla tak wykonanych betonów przeprowadzono badanie wytrzymałości na ściskanie według PN-EN 12390-3[4] oraz badanie karbonatyzacji metodą przyspieszoną według PN-EN 12390-12[5], a także wyznaczono współczynnik migracji jonów chlorkowych zgodnie z PN-EN 12390-18[6].
Wyniki wytrzymałości na ściskanie przedstawiono w tabeli 4.

Tabela 4. Wytrzymałość na ściskanie
Klasa wytrzymałości C25/30 została uzyskana przez beton na cemencie portlandzkim popiołowym po 28 dniach, a na cemencie pucolanowym po 56 dniach dojrzewania. Klasa C30/37 została uzyskana przez beton wykonany na CEM II/B-V 42,5 R-HSR/NA po 56 dniach dojrzewania.
Badanie karbonatyzacji obydwu betonów rozpoczęto po 28 dniach dojrzewania w wodzie oraz 14 dniach w komorze klimatycznej o wilgotności 50–65%.
Wyniki karbonatyzacji w postaci maksymalnej głębokości, jak również jej prędkości (stopień karbonatyzacji Kac) przedstawiono na rysunku 6. Współczynnik kierunkowy funkcji liniowej przedstawia prędkość karbonatyzacji Kac. Współczynnik dopasowania funkcji liniowej spełnia wymagania normy PN-EN 12390-12[5], wynosi minimum 0,95.
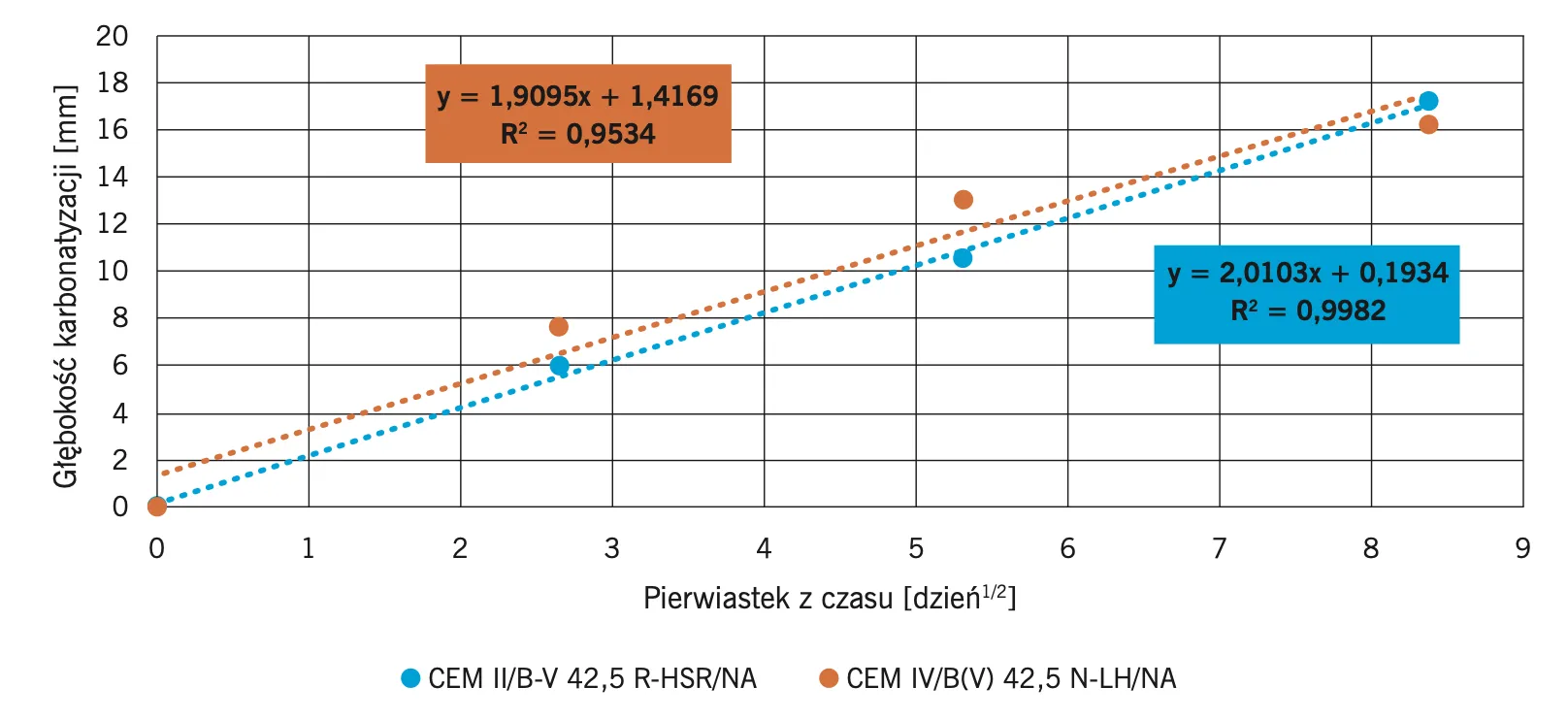
Rys. 6. Wyniki badań karbonatyzacji metodą przyspieszoną
Uzyskane wyniki pokazują, że beton wykonany z użyciem cementu CEM IV/B (V) 42,5 N-LH/NA wykazuje nie gorszą, a wręcz lepszą odporność na karbonatyzację niż jego odpowiednik na cemencie CEM II/B-V 42,5 R-HSR/NA. Świadczay o tym mniejsza głębokość karbonatyzacji, która wyniosła 16 mm, oraz prędkość – 1,91 mm/dzień1/2. Badanie migracji jonów chlorkowych rozpoczęto po 56 dniach dojrzewania betonów w wodzie. Wyniki przedstawiono na rysunku 7.
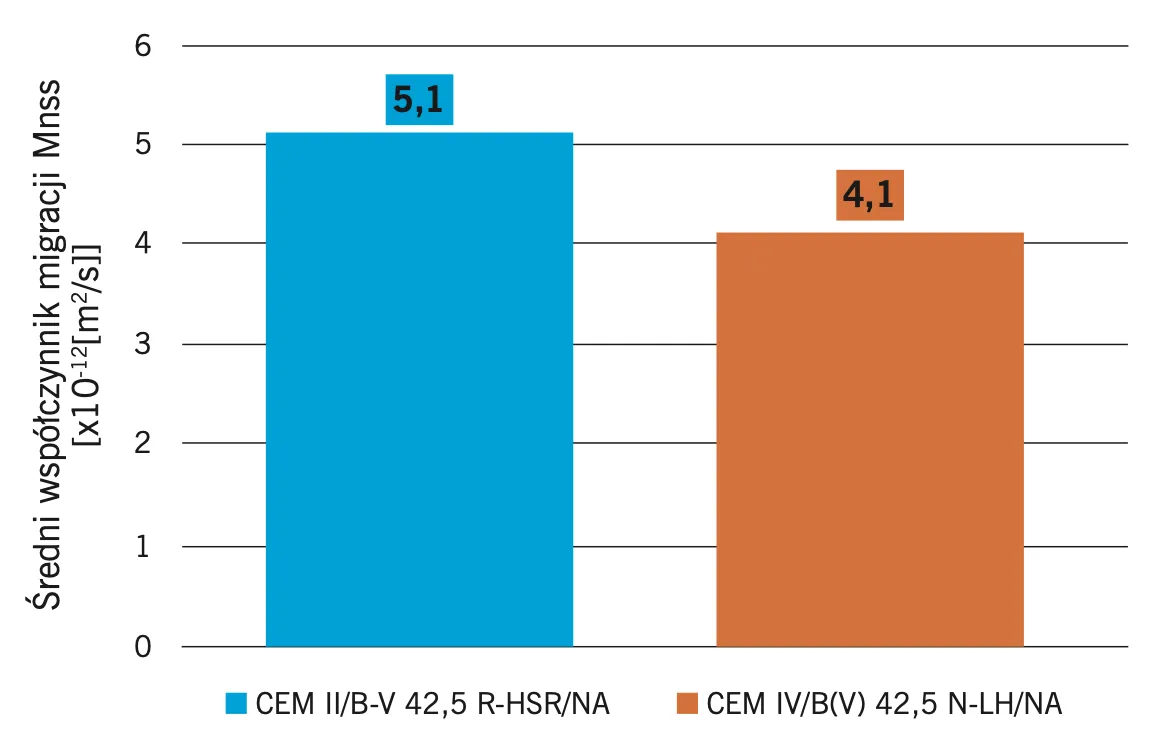
7. Wyniki badań współczynnika migracji jonów chlorkowych
Przedstawione wyniki wskazują, że beton na cemencie pucolanowym charakteryzuje się większą szczelnością, reprezentowaną przez niższy o ok. 20% współczynnik migracji jonów chlorkowych.
Badanie ekspansji w środowisku siarczanowym
Cement CEM IV/B (V) 42,5 N-LH/NA nie jest oznakowany jako odporny na siarczany (HSR). Dlatego aby móc go zastosować w klasie ekspozycji XA2 oraz XA3, wykonano badania ekspansji zaprawy na tym cemencie w środowisku siarczanowym. Badanie wykonano zgodnie z normą PN-B-19707[7]. Wyniki badań ekspansji zaprawy przedstawiono na rysunku 8.
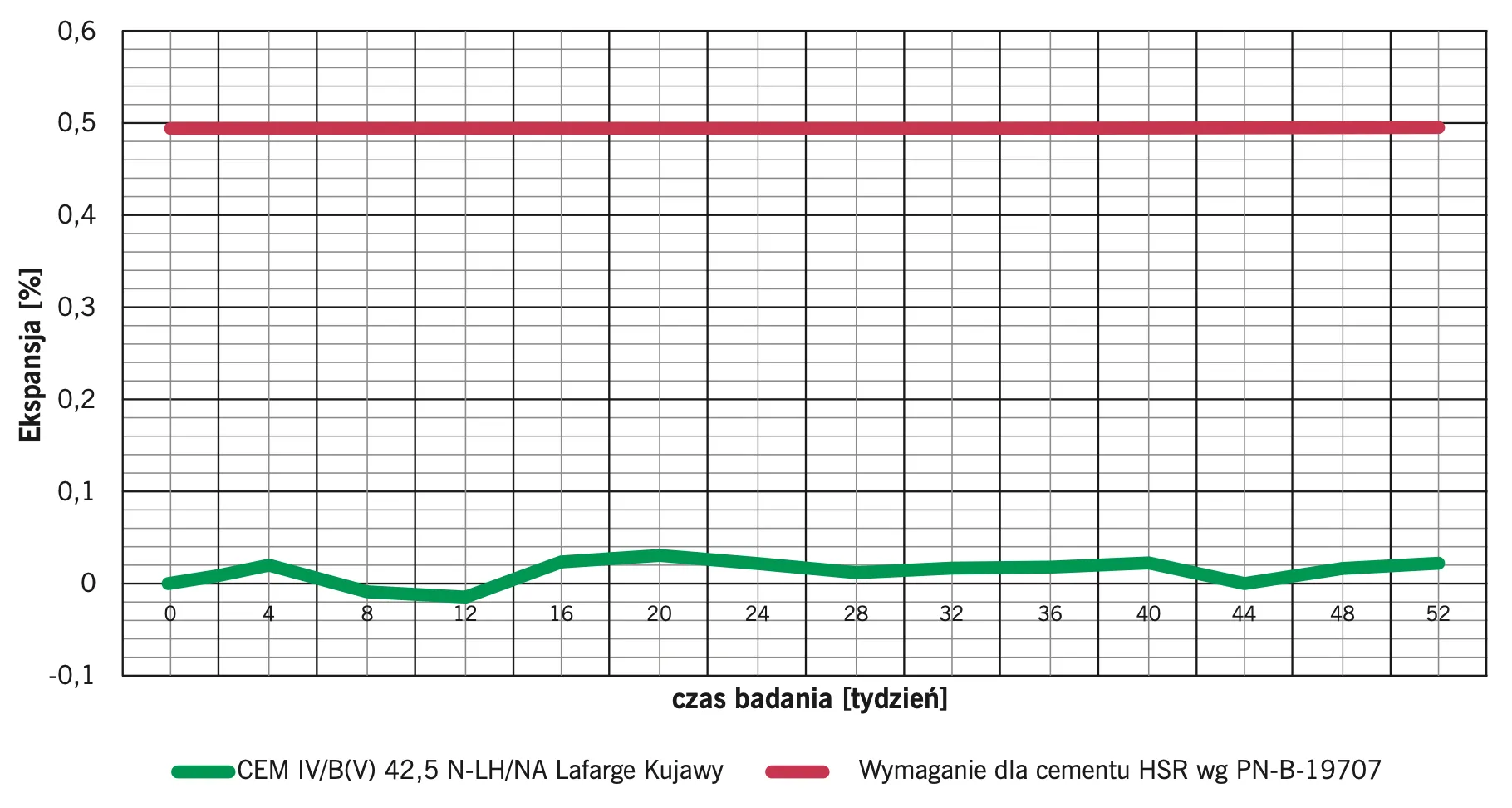
8. Wyniki badań ekspansji zaprawy w roztworze NA2SO4
Uzyskane wyniki badań dla CEM IV/B (V) 42,5 N-LH/NA spełniają wymagania normy [7] z dużym zapasem, tzn. ekspansja badana po 52 tygodniach jest mniejsza niż 0,5%. Badania jednoznacznie pokazują, że cement ten może być z powodzeniem zastosowany w klasach ekspozycji XA2 oraz XA3.
W niniejszym artykule odnieśliśmy się do holistycznego spojrzenia na ślad węglowy materiałów budowlanych jako składową śladu węglowego emitowanego przez budynki, omówiliśmy cementy niskoklinkierowe jako spoiwo do produkcji betonu, oraz pokazaliśmy, że produkcja betonów niskoemisyjnych na tych spoiwach jest możliwa i spełnia wszelkie kryteria normalizacji w tym obszarze.
Kolejnym krokiem w dekarbonizacji, do którego chcieliśmy nawiązać, są wszelkie technologie wychwytywania CO2 już na etapie „komina cementowni”. Ich celem jest pełna dekarbonizacja produkcji cementu. Projekty typu CCS (carbon capture and storage) powstają już w naszym kraju i za chwilę będą wspierały przemysł cementowy w jego dekarbonizacji. Będzie to możliwe dzięki nowym technologiom, m.in. CryocapTMFG.
Przewiduje się, że od 2027 r. emisja w sektorze cementowym w Polsce będzie niższa o 10% (przechwycone zostanie 10% CO2). Pomoże nam w tym m.in. innowacyjna technologia wychwytywania i oddzielania dwutlenku węgla z gazów emitowanych do atmosfery z instalacji podczas procesu wypału klinkieru. Następnie oddzielony dwutlenek węgla zostanie skroplony w niskiej temperaturze (jest to proces kriogeniczny). Metoda ta pozwala na wyekstrahowanie 99,9% czystego dwutlenku węgla. Skroplony dwutlenek węgla będzie transportowany do magazynów zlokalizowanych na Morzu Północnym, tam zostanie wtłoczony do wyeksploatowanych pól naftowych lub gazowych, gdzie będzie składowany na stałe. Schemat ideowy instalacji zaprezentowano na rysunku 9.
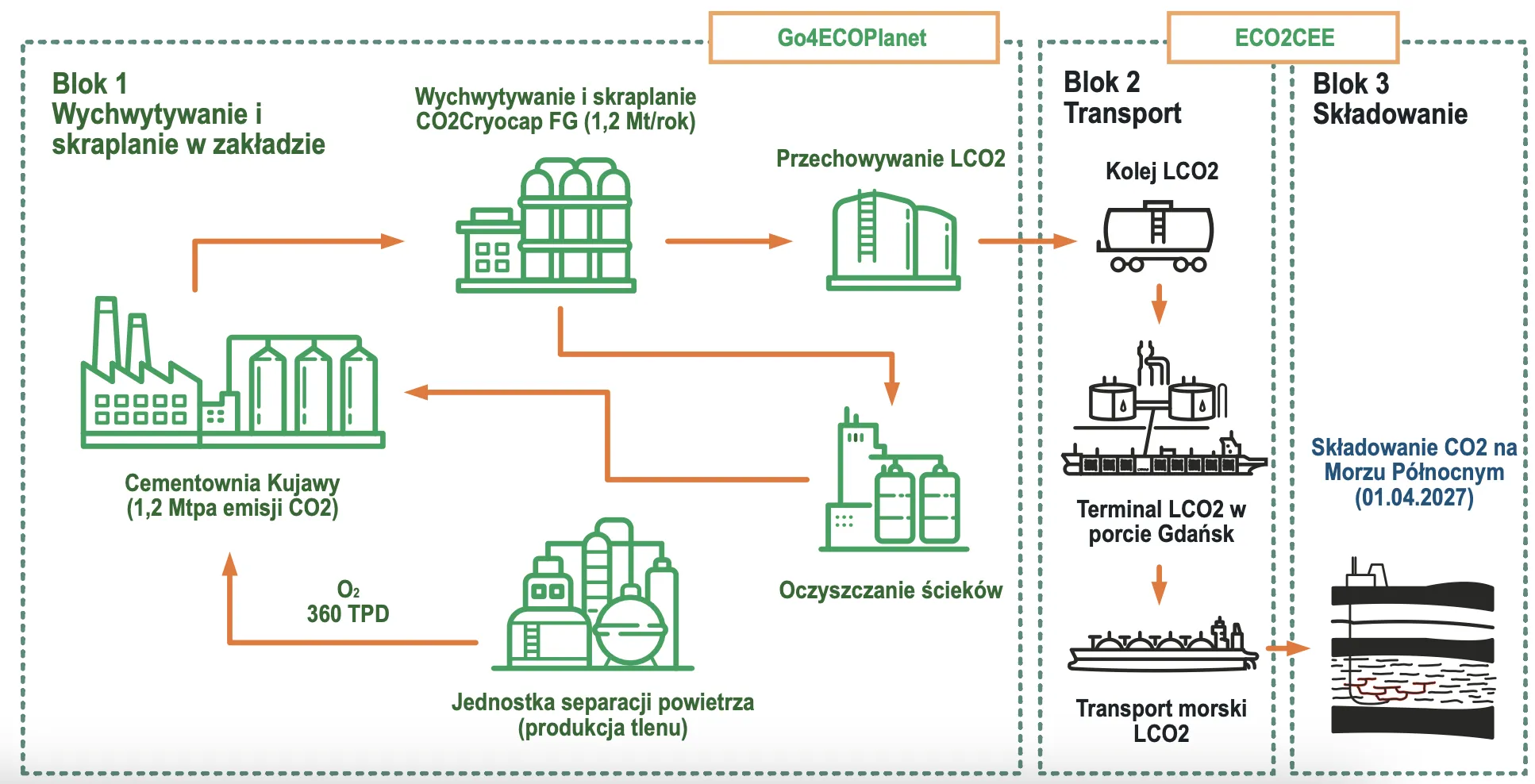
Rys. 9. Schemat ideowy instalacji do wychwytywania CO2 projektu CCS (carbon capture and storage)
Wnioski
Ślad węglowy materiałów budowlanych w pewnej części jest pochodną struktury paliw używanych do ich produkcji oraz źródeł pochodzenia energii elektrycznej – od tego wszystko się zaczyna i tu jest pierwsza lekcja do odrobienia. Materiały budowlane ogółem stanowią 20-30% śladu węglowego wznoszonych budynków, pozostała część (około 70%) dotyczy fazy użytkowania i utrzymania budynku. Dwa materiały generujące największy ślad węglowy w procesie wznoszenia budynków to beton i stal. Skupienie się na redukcji śladu węglowego w tym obszarze może przynieść nam największe korzyści (do 30% redukcji dla betonu i około 25% dla wszystkich materiałów budowlanych). Wymiana betonu na niskoemisyjny w przypadku naszego case study spowodowała redukcję śladu węglowego o 899 919 kg e CO2, co stanowi oszczędność na poziomie 62,5 kg e CO2/m2. W pierwszej kolejności należy optymalizować największe elementy konstrukcji, takie jak płyta fundamentowa. Przyniesie to nam najwięcej korzyści w końcowym rozliczeniu. Po wykonaniu wszelkich możliwych optymalizacji na poziomie materiałów budowlanych nadal mamy przestrzeń do optymalizacji i zagospodarowania ok. 70% emisji operacyjnej pochodzącej z fazy utrzymania i użytkowania. Przedstawione w artykule wyniki badań autorów świadczą o tym, że możliwe jest wykonanie betonów niskoemisyjnych – przy użyciu cementów niskoklinkierowych – charakteryzujących się nie gorszą, a wręcz lepszą trwałością niż ich odpowiedniki wyprodukowane na cemencie, np. CEM II/B-V 42,5 R-HSR/NA. Osiągnięcie tego celu wymaga jednak dużego zaangażowania producentów cementu i betonu w proces badań laboratoryjnych, aby z jednej strony budować bazę wiedzy dotyczącą uzyskiwanych trwałości dla coraz to nowych rodzajów cementu, z drugiej – wyznaczać zależności pomiędzy zmiennymi w produkcji cementu i betonu w taki sposób, aby móc dokładniej przewidywać właściwości produktu końcowego. Niezmiernie istotne z punktu widzenia trwałości wykonanych elementów jest również świadome i odpowiedzialne podejmowanie przez wykonawców decyzji o wydłużonym procesie pielęgnacji konstrukcji wykonanych przy użyciu cementów niskoklinkierowych.
W najbliższych latach liderzy rynku w obszarze cementu i betonu będą w dalszym ciągu koncentrować się na innowacyjnych technologiach modernizujących cały przemysł cementowy, w tym efektywniejszym spalaniu paliw alternatywnych i wychwytywaniu GHG oraz jeszcze lepszym i skuteczniejszym wykorzystywaniu cementów niskoklinkierowych w produkcji betonów konstrukcyjnych.
Literatura
- PN-EN 197-5:2021-07 Cementy – Część 5: Cement portlandzki wieloskładnikowy CEM II/C-M i cement wieloskładnikowy CEM VI.
- PN-EN 206+A2:2021-08: Beton – Wymagania właściwości użytkowe, produkcja i zgodność.
- PN-B-06265:2022-08: Beton – Wymagania, właściwości użytkowe, produkcja i zgodność. Krajowe uzupełnienie PN-EN 206+A2:2021-08.
- PN-EN 12390-3:2019-07: Badania betonu – Część 3: Wytrzymałość na ściskanie próbek do badań.
- PN-EN 12390-12:2020-06: Badania betonu – Część 12: Oznaczanie odporności betonu na karbonatyzację – Przyspieszona metoda karbonatyzacji.
- N-EN 12390-18:2021-08: Badania betonu – Część 18: Oznaczanie współczynnika migracji chlorków.
- PN-B-19707:2013-10: Cement. Cement specjalny. Skład, wymagania i kryteria zgodności.
Autorzy:
Dariusz Kuryś, Michał Drabczyk
Holcim Cement SA